Introduction to the Principle of Baking Paint for Hardware Accessories in Apparel and Leather Goods
I. Preface
In the production of apparel and leather goods, hardware accessories play a crucial role in enhancing the overall aesthetic and functionality. One of the common finishing processes for these hardware accessories is baking paint. This technique not only gives the hardware a beautiful and durable appearance but also protects it from corrosion and wear. In this article, we will explore in detail the principle of baking paint for hardware accessories related to apparel and leather products, covering aspects such as its basic concept, the materials involved, the process steps, and the chemical reactions taking place.
II. Basic Concept of Baking Paint
Definition
Baking paint, also known as stoving enamel or heat-cured paint, is a type of paint that requires a specific heating process to cure and form a hard, durable coating on the surface of an object. For hardware accessories in the apparel and leather industry, it is applied to items like buckles, zippers, studs, and various decorative metal parts.
Purpose
The main purposes of using baking paint on these hardware accessories are multi-fold. Firstly, it provides an attractive visual effect, allowing for a wide range of colors and finishes to match different styles of apparel and leather goods. Secondly, it improves the wear resistance of the hardware, making it able to withstand the friction and impacts during daily use. Thirdly, it offers good corrosion resistance, protecting the metal from oxidation and rusting, especially when these accessories may be exposed to moisture or other environmental factors.
III. Materials Involved in Baking Paint
Paint Components
1. Resin: The resin is the main film-forming component in the baking paint. Commonly used resins include acrylic resins, polyester resins, and epoxy resins. For example, acrylic resins are favored for their good transparency, weather resistance, and ability to provide a smooth finish. They are often used when a bright and durable coating is required for hardware accessories that are visible on apparel or leather items.
2. Pigments: Pigments are responsible for imparting color to the paint. They can be inorganic pigments like titanium dioxide (which is widely used for its excellent whiteness and hiding power) or organic pigments that offer a broader range of vivid colors. Different pigments are carefully selected based on the desired color of the hardware accessories, whether it's a classic black, a trendy metallic hue, or a bright and eye-catching color to match a specific fashion design.
3. Solvents: Solvents are used to dissolve the resin and pigments, making the paint have a suitable viscosity for application. They also help in the leveling of the paint film during the drying process. However, with the increasing emphasis on environmental protection, there has been a shift towards using water-based solvents or low-volatile organic compound (VOC) solvents to reduce air pollution and meet strict environmental regulations.
Substrates (Hardware Materials)
The hardware accessories for apparel and leather goods are usually made of metals such as zinc alloy, copper, or stainless steel. Zinc alloy is commonly used due to its good castability and affordability, which allows for the production of various intricate shapes of buckles and decorative elements. Copper offers excellent electrical conductivity and a warm, attractive appearance, while stainless steel is renowned for its high corrosion resistance and strength, often used for more durable and high-end hardware parts.
IV. Process Steps of Baking Paint
Pretreatment of Hardware
1. Cleaning: The first step is to thoroughly clean the hardware accessories to remove any dirt, grease, or oxides on the surface. This can be achieved through methods like ultrasonic cleaning in a suitable cleaning solution or using chemical cleaners. For example, if there is oil residue from the manufacturing process on a metal buckle, it needs to be completely removed to ensure good adhesion of the paint.
2. Surface Treatment: Depending on the metal substrate, additional surface treatment may be required. For zinc alloy parts, a phosphate conversion coating may be applied to improve the adhesion of the paint and enhance corrosion resistance. Stainless steel may undergo passivation treatment to further protect its surface and make it more receptive to the paint layer.
Paint Application
1. Spraying: One of the most common methods of applying baking paint to hardware accessories is spraying. This allows for an even distribution of the paint over the complex shapes of the accessories. Special spraying equipment is used, which can adjust the spray pressure and atomization degree to ensure a smooth and uniform paint film. For example, when painting a decorative metal stud with a textured surface, careful spraying is needed to cover all the recesses and protrusions evenly.
2. Dipping: In some cases, dipping the hardware into a paint bath can also be used, especially for small and simple-shaped accessories. This method ensures complete coverage of the part with paint but requires proper draining and drying to avoid uneven thickness or drips.
Baking Process
1. Drying and Curing: After the paint is applied, the hardware accessories are placed in an oven for the baking process. The temperature and time settings are crucial and vary depending on the type of paint and the substrate. Generally, the temperature can range from around 120°C to 200°C, and the baking time may be from 15 minutes to several hours. During this process, the solvents in the paint evaporate, and the resin undergoes a chemical cross-linking reaction, which hardens the paint film and makes it adhere firmly to the metal surface. For instance, an acrylic resin-based baking paint on a zinc alloy buckle may require a baking temperature of about 150°C for 30 minutes to achieve optimal curing and a durable finish.
2. Cooling: After baking, the hardware is allowed to cool down naturally or in a controlled cooling environment. This helps to stabilize the paint film and ensures that it has the desired mechanical properties and appearance.
V. Chemical Reactions in Baking Paint
Evaporation of Solvents
During the initial stage of the baking process, the solvents in the paint start to evaporate due to the heat. This is a physical change that turns the liquid paint into a more viscous state as the solvents escape. As the temperature rises, the rate of evaporation increases, and the paint film gradually thickens on the surface of the hardware. For example, if a solvent-based baking paint contains xylene as a solvent, xylene will vaporize and leave the paint film during the baking process, reducing the fluidity of the paint and starting the formation of the solid coating.
Cross-linking of Resin
The key chemical reaction in baking paint is the cross-linking of the resin. Different resins have their specific cross-linking mechanisms. For example, in the case of polyester resins, under the influence of heat and sometimes with the help of curing agents, the functional groups in the resin molecules react with each other to form a three-dimensional network structure. This cross-linking not only increases the hardness and strength of the paint film but also improves its resistance to chemicals, abrasion, and environmental factors. Similarly, epoxy resins undergo polymerization reactions during baking, where the epoxy groups react with curing agents like amines to create a highly cross-linked and durable coating on the hardware surface.
Pigment Fixation
The pigments in the paint are also affected by the baking process. As the resin cross-links and the paint film solidifies, the pigments are trapped within the resin matrix and become firmly fixed. This ensures that the color remains stable and does not fade or bleed over time. The chemical bonds formed between the resin and the pigments during the cross-linking process contribute to the long-term colorfastness of the hardware accessories, maintaining their attractive appearance even after repeated use and exposure to sunlight or other external elements.
VI. Quality Control and Testing of Baked Paint on Hardware
Appearance Inspection
After the baking paint process, the hardware accessories are visually inspected for any defects such as uneven color, orange peel texture (a rough, bumpy surface similar to that of an orange peel), or paint runs. Operators use proper lighting conditions and inspection tools to check the overall appearance and ensure that it meets the aesthetic requirements of the apparel or leather goods they will be used on.
Adhesion Testing
To evaluate the adhesion of the paint film to the hardware substrate, methods like the cross-cut test or the tape test are employed. In the cross-cut test, a grid pattern is cut into the paint film with a sharp tool, and then adhesive tape is applied and removed. If the paint film remains intact or only a minimal amount of paint flakes off, it indicates good adhesion. This is crucial because poor adhesion can lead to the paint peeling off during use, affecting the durability and appearance of the hardware.
Corrosion Resistance Testing
Hardware accessories with baked paint are often subjected to corrosion resistance tests, such as salt spray tests. In a salt spray chamber, the painted hardware is exposed to a mist of salt solution for a specified period, simulating harsh environmental conditions. After the test, the hardware is examined for signs of rust or corrosion on the metal surface under the paint film. Good baking paint should provide sufficient protection to prevent or minimize such corrosion, ensuring the long-term usability of the hardware in various environments.
VII. Conclusion
The principle of baking paint for hardware accessories in apparel and leather goods involves a combination of carefully selected materials, precise process steps, and complex chemical reactions. Understanding these aspects is essential for manufacturers to produce high-quality hardware with excellent aesthetic and functional properties. By continuously improving the baking paint process and controlling the quality through proper testing methods, the industry can ensure that the hardware accessories not only enhance the beauty of apparel and leather products but also withstand the rigors of daily use and environmental exposure, contributing to the overall quality and durability of these consumer goods. As fashion trends evolve and consumer demands for better quality increase, further research and innovation in baking paint technology for hardware will continue to play a vital role in the development of the apparel and leather goods industry.


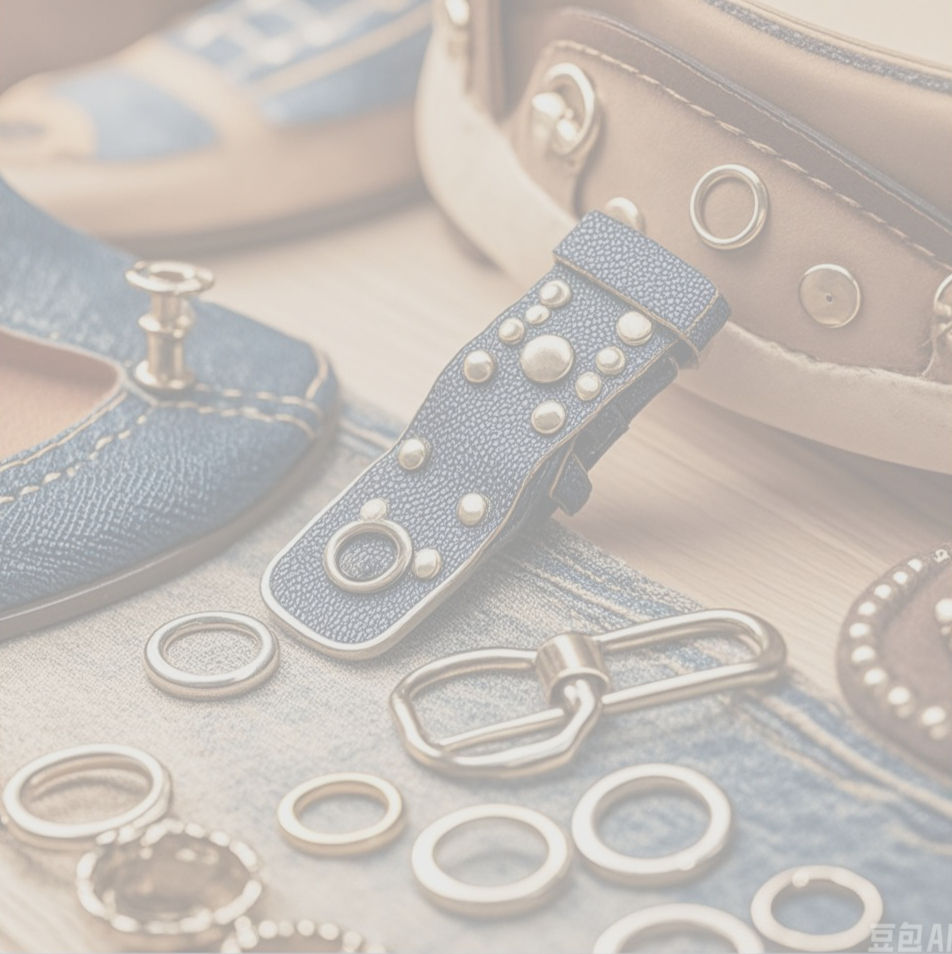
Surface Finishes | Paint Coatings
A professional manufacturer of snap fasteners, studs, rivets, buttons, buckles, grommets,metal tags,zipper sliders & pulls,garment accessories and fashion ornaments.